With a heritage spanning over 75 years, Bailey of Bristol is the UK’s longest-established independent leisure vehicle manufacturer. As a family-owned business, Bailey has become the Nation’s Favourite brand, accounting for approximately one in three new caravan sales in the UK and now expanding into the motorhome and campervan markets.
To future-proof its production and address challenges caused by ageing machinery, Bailey of Bristol recently made a significant investment in HOMAG technology. This included five CENTATEQ N-510 CNC machines and two STORETEQ P-500 storage and retrieval systems, marking a huge operational upgrade designed to streamline production, improve efficiency, and support the company’s long-term growth.
The need for advanced technology
Prior to the investment, Bailey was operating seven CNC machines that were over 20 years old. These machines were frequently breaking down, leading to increased repair and maintenance costs. Additionally, they required manual loading which presented health and safety concerns while slowing down production.
“The old machines were a bottleneck, and, in all honesty, they were holding the business back,” explains Lee Barrett, Production Manager at Bailey of Bristol. “We needed a solution that would not only improve efficiency but also create a safer working environment for our team. The decision was made to replace the seven aging machines with five new CNCs and two automated storage systems.”
Choosing HOMAG
Bailey embarked on a thorough vetting process, evaluating three leading machinery suppliers. The selection process began at Ligna, the international trade fair for woodworking and processing technology, where Bailey presented its production requirements to potential suppliers. HOMAG stood out due to its proactive approach and deep understanding of Bailey’s needs.
“Phil Pitchford, the UK CNC Product Manager at HOMAG, was instrumental in the decision,” Lee noted. “Him and his team immediately took the initiative, analysing our production needs and recommending the most effective solutions. We remained open-minded throughout, even sending sample products to each supplier for testing. We also travelled to Germany to see the machines in action. Ultimately, HOMAG emerged as the number one choice.”
A key factor in HOMAG’s success was the STORETEQ P-500’s twin bridge system, a unique feature that ensures a continuous material flow. “Our biggest concern was finding a storage system that could keep up with CNC production. The STORETEQ P-500 was the only machine of its kind to offer twin bridges, with which you can consume the stock and refill it in a single shift, eliminating the need for extra hours just to manage stock levels – a massive time saver.”
Software integration for greater control
Bailey also implemented HOMAG’s woodStore software, which significantly improved stock control and production management. “Before, each CNC had to be manually loaded, placing all the onus on the operator,” Lee said. “Now, all five CNCs are controlled and loaded from the office, improving efficiency and oversight. We’re also working with HOMAG to implement productionManager software to further expand our capabilities.”
Installation and training
Despite a few hurdles in the run up to installation, HOMAG’s project management team ensured that everything was completed on time, with minimal disruption to production. “The communication throughout the process was excellent,” Lee commented, “and the installation itself went very smoothly. HOMAG then got our operators up to speed and has continued to provide ongoing support as we adapt to the new technology, with further in-depth training scheduled in the near future.”
The impact of the investment
The new machines have transformed Bailey’s production process, delivering improvements across multiple areas. “The most noticeable benefit is the time savings,” Lee explains. “As mentioned, with the STORETEQs having two bridges, we have cut our hours significantly. This combined with the capabilities of the CNCs has made us so much more efficient.
“Then there’s the health & safety side of things. The machines do all the manual lifting, and it’s all safety barriered off, so the operators are kept a safe distance from any potential hazard. It’s also improved the general mental health of the team, mainly because no-one has to work overtime!
“Control wise, as mentioned, we’ve got the software that allows us to manage everything from the office, so we’ve got a lot more visualisation of what’s going on. And in terms of production, even though we are now running two fewer CNCs and one less shift a day, our output has increased significantly.
“Quality has improved as well; we’re seeing a lot less damage with the CENTATEQ N-510s, and the accuracy is phenomenal. Our costs are down and we’re wasting substantially less material, which is better for the environment as well as our business.”
Above and beyond
Reflecting on the experience, Lee praised HOMAG’s dedication and support. “HOMAG has been fantastic from start to finish. They took the time to fully understand our needs and have been extremely accommodating.
“For instance, our facility’s ceiling height is slightly lower than what is required for a STORETEQ … so HOMAG actually redesigned the machine, enabling it to fit. That was service beyond what we’d ever expect from a supplier!
“With the machines now up and running, we have full confidence that whenever we contact them with an issue, we will get a prompt resolution. We have numerous different contacts within HOMAG, all of whom are always happy to help. We can’t ask for much more.”
Looking to the future
Bailey’s investment in HOMAG technology has unlocked new opportunities for growth. “There’s no denying that our previous machines were placing limitations on the business – when you’re running three shifts (24 hours) a day, there’s really not a lot more you can do,” Lee stated. “Now, we operate far superior machines across just two shifts, giving us room to expand our portfolio and production volumes. With HOMAG’s support, we’re well-positioned to continue growing Bailey of Bristol for years to come.”
For more information or a demonstration of any of the HOMAG machinery and software, contact Adele Hunt at HOMAG UK on 01332 856424.
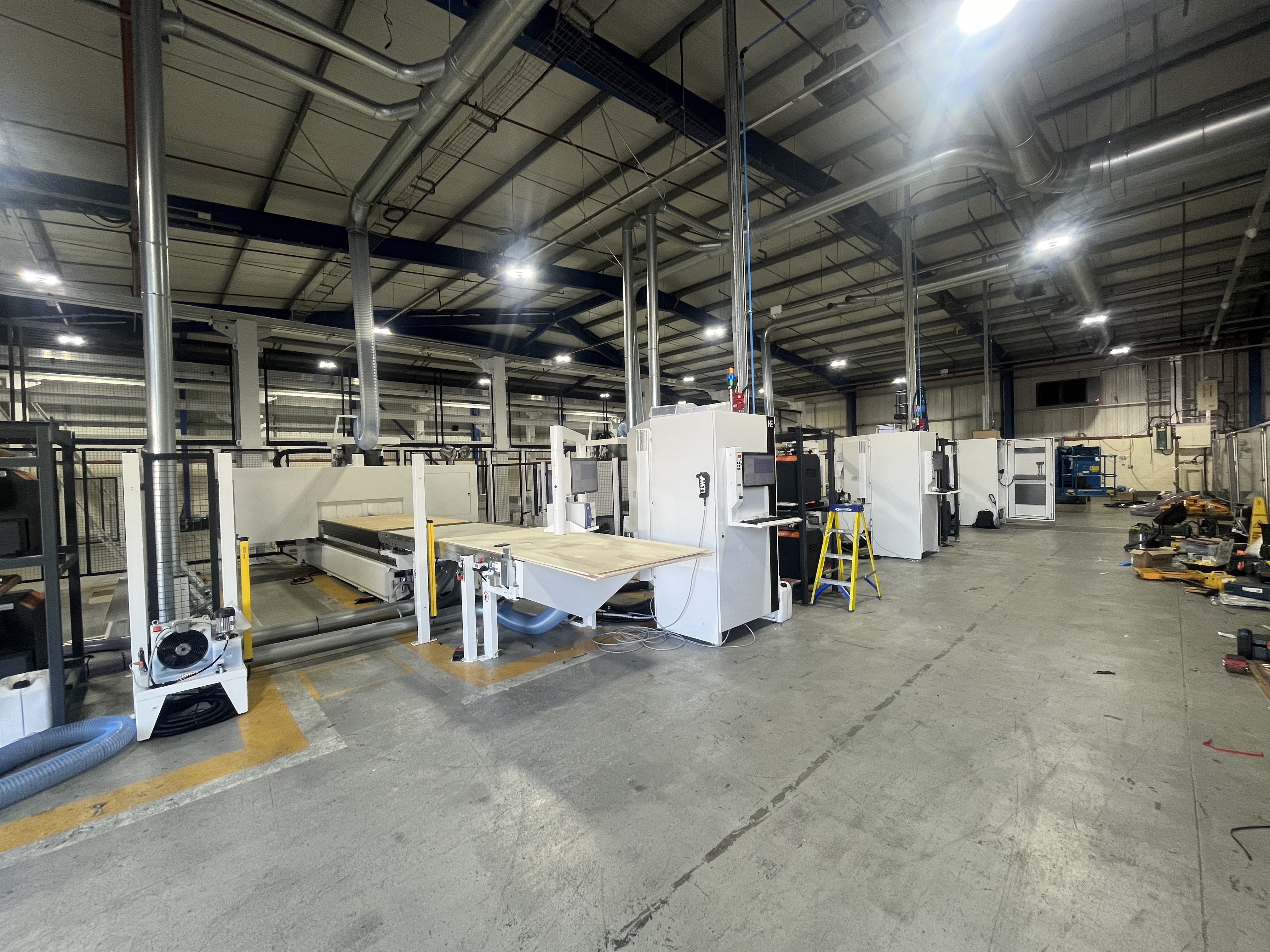