Standing at an impressive 17.8m tall, the Black & White Building is an artful example of timber construction. Aside from its concrete foundations and a slab, everything bar the connections is made of timber ...
The client – workspace providers, The Office Group – required an office space with built-in adaptability, and one which allowed for future layout changes, at a site in Shoreditch, East London.
When The Office Group first acquired the site, it had planning permission for a new-build office space. The site had two existing buildings on it, one of which was a timber building, about 115 years old, that had been a curing shed for an old timber company; behind it was a 1970s concrete and steel building.
The possibility of refurbishment was examined, but, unfortunately, proved not to be viable. As such, The Office Group were concerned about the embodied carbon cost of the new building. Despite having an in-house team of designers, the group’s preference is to collaborate with external architects. For this particular project, its long-term collaborators, Waugh Thistleton Architects, were selected, and provided a solution centred upon engineered timber.
The structure
The Black & White Building’s structure comprises a frame made of a beech-based laminated veneer lumber (LVL), with cross-laminated timber (CLT) floor slabs and core. 872 pieces of timber were used in the building, and arrived by truck before being craned into place.
“It is primarily the strength and stability of the LVL that provides the structural frame with strength comparable to one made of steel,” explains Andrew Waugh. “Yet the structure weighs some 20 to 30 per cent less than a comparable concrete one.”
The beech LVL in the frame’s beams and columns was sourced from near Frankfurt and is “equivalent in strength to C50/60 concrete”. This allows the frame to take all the gravitational load, while the softwood CLT of the floor slabs and core provide the shear capacity.
Moisture management
One challenge for any timber building is dealing with water, and thus, numerous precautions were taken to avoid any potential water ingress.
The roof has an inherent fall to it and, at the building’s completion, had tapered gutters to direct water to outlets.
The CLT in the floor slabs in the bathrooms – which are located next to the core on each floor – were removed. This was replaced by joists and plywood, which not only satisfied the insurers, but was also cheaper.
Interior
‘An adaptable building is a sustainable one’ was a key concept behind the design. There are no structural internal partition walls in the Black & White building, so the workspaces are large and open.
Additional space was gained by services being inlaid into the LVL beams, leaving plenty of opportunity for layout customisation in any alternative future uses of the building.
Windows are openable throughout, and timber is left exposed almost everywhere internally, with even the main staircase being timber.
As the most comprehensive supply chain body for timber in the UK, TDUK is a crucial resource that connects, inspires and supports more than 1500 businesses to “build a better world through wood” For further details of this project, and access to TDUK’s full library of 174 technical case studies, sign up for free on its website.
Client: The Office Group
Architect: Waugh Thistleton Architects
Structural Engineer: Eckersley O’Callaghan
Structural Timber Engineer: Engenuiti
Main Contractor: MidGroup/Parkeray
Wood Supplier: Züblin Timber; Pollmeier; Pacegrade
Timber Frame: Hybrid Structures
Species: Whitewood, European; Beech, European & Tulipwood
Photography: Jake Curtis
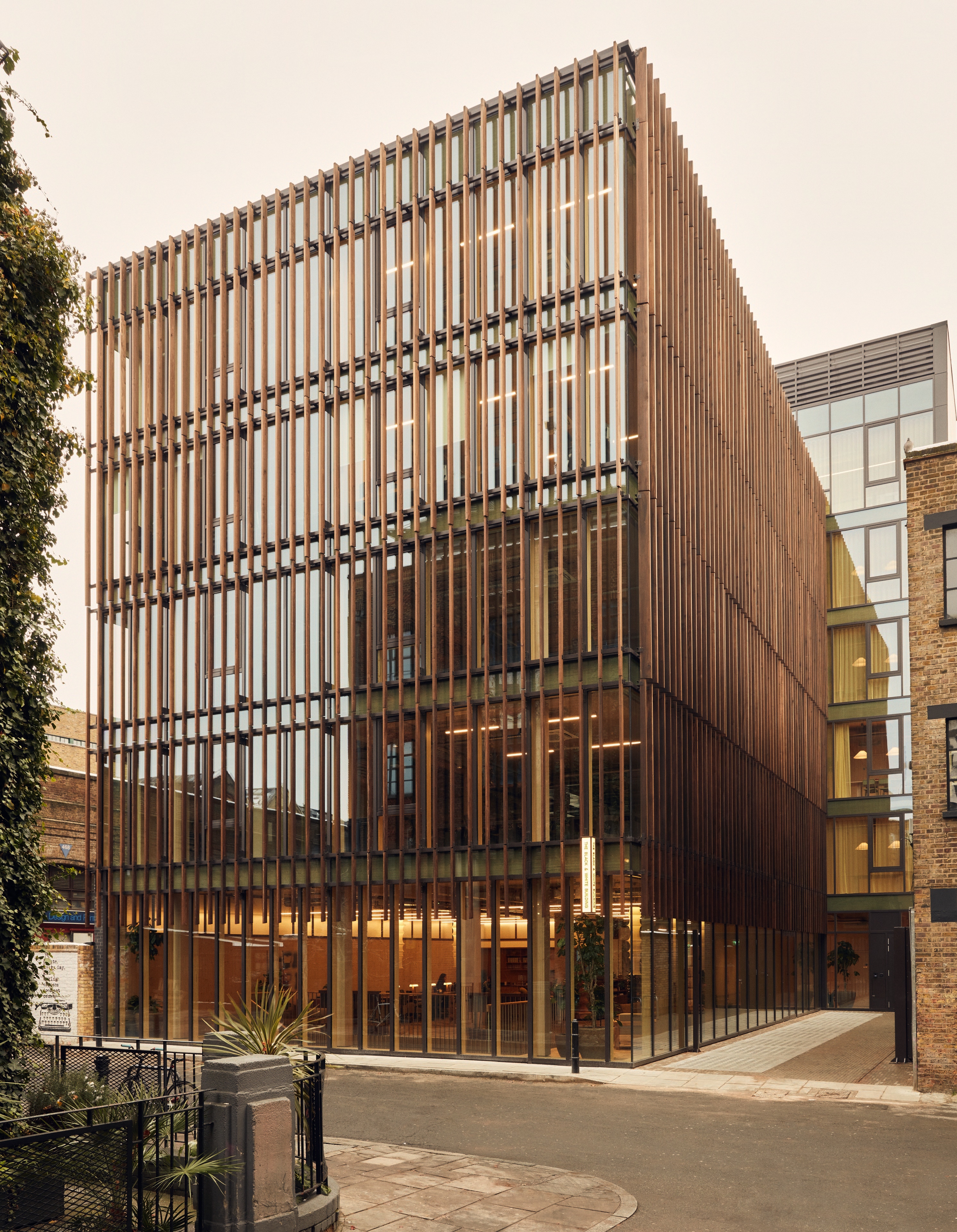
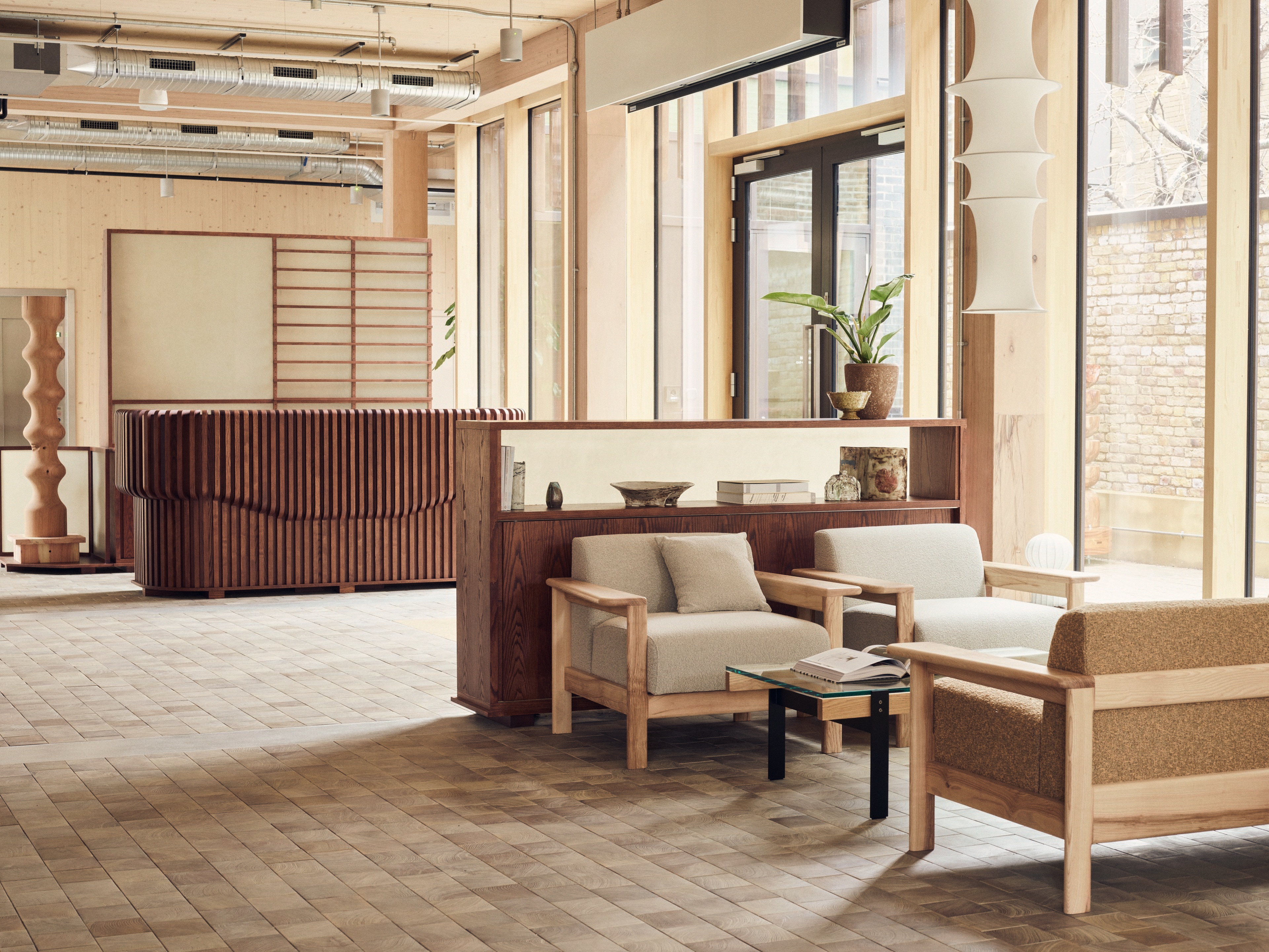
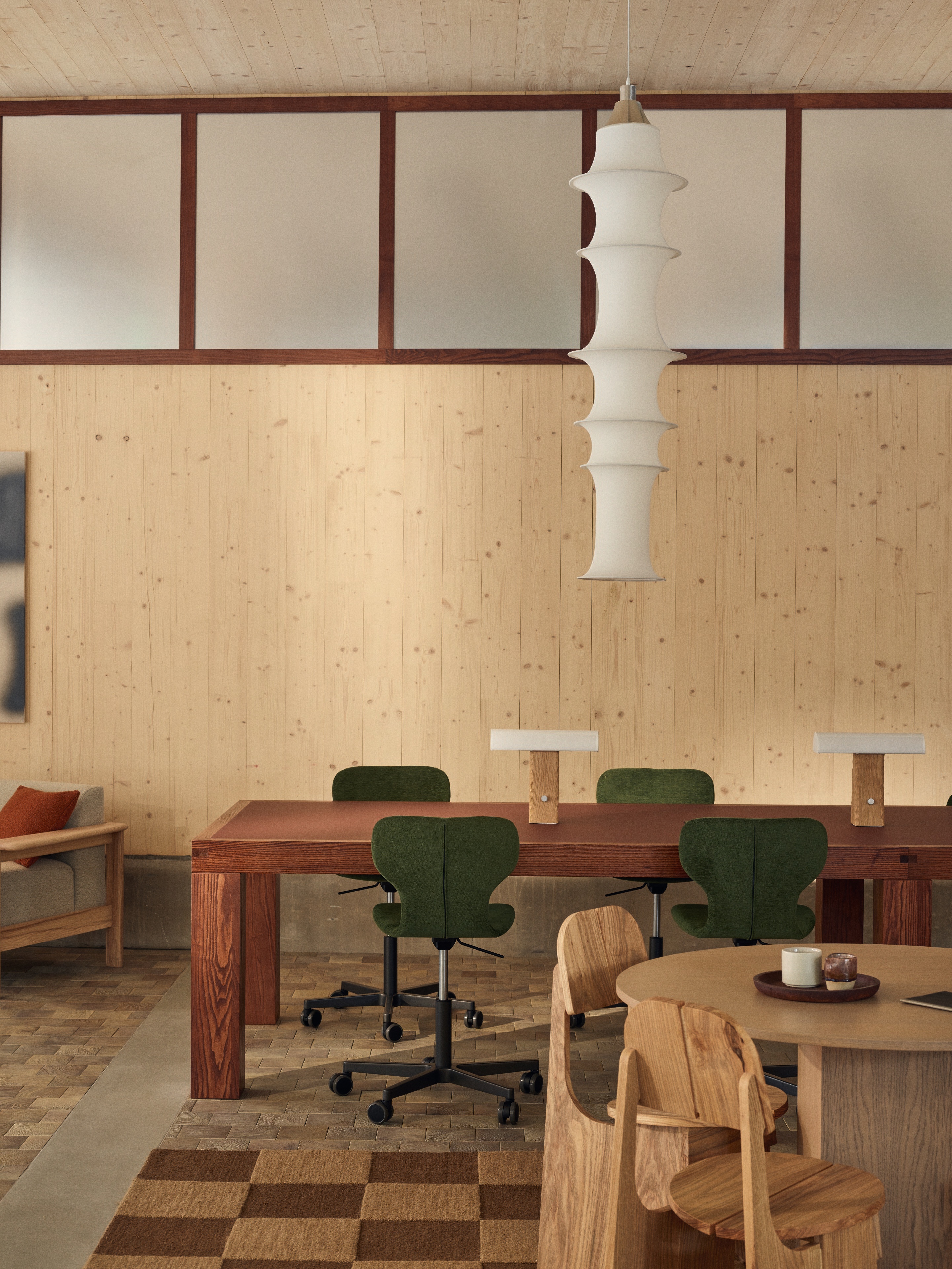
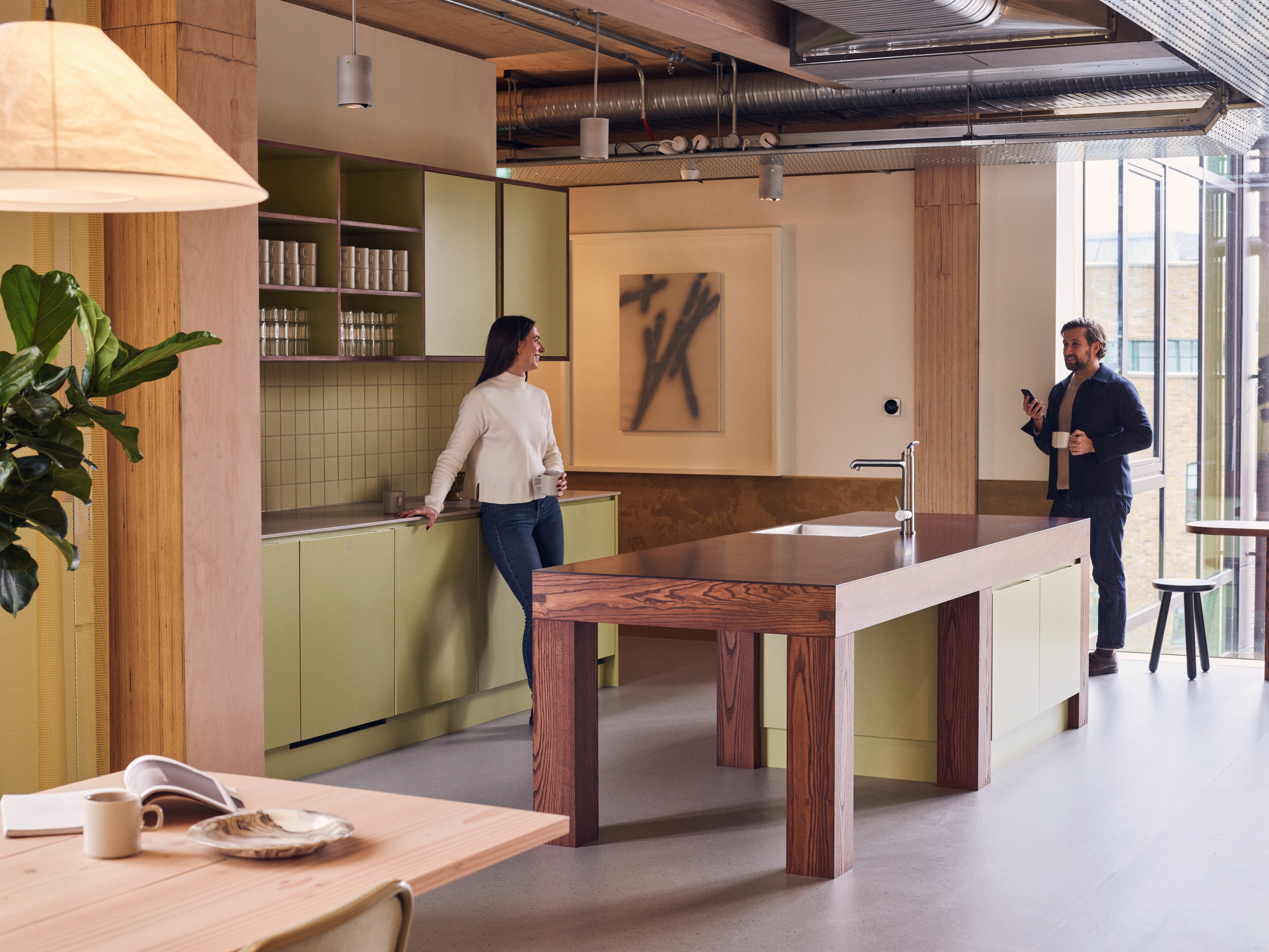
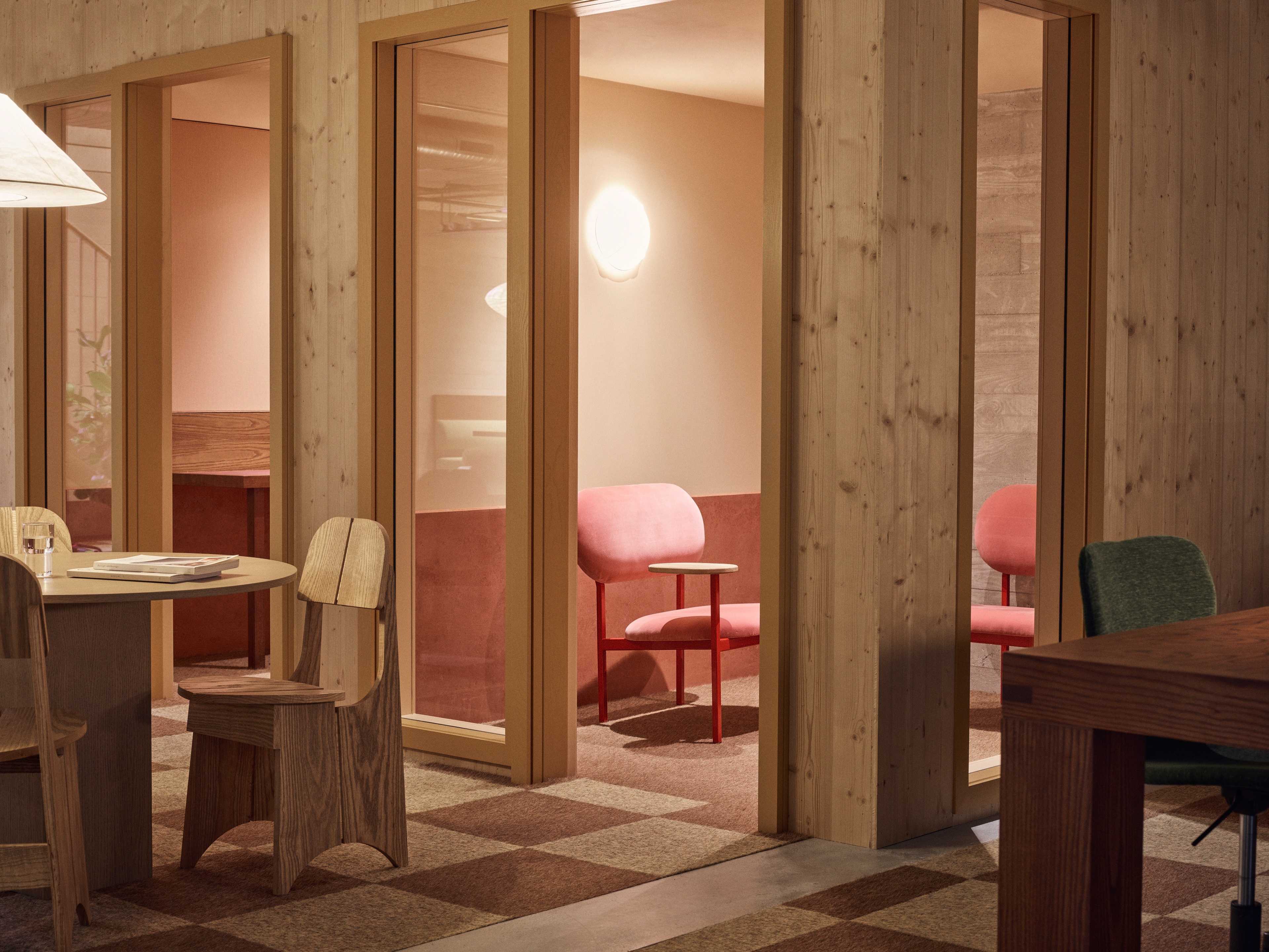