As a leading UK manufacturer of fire safety doors and screens, Northern Fire Solutions Ltd ensures compliance and safety for its clients across the private and public sectors. With a reputation for high-quality, certified products, the company constantly seeks ways to improve its operations, and is currently undergoing a full-scale digital transformation to achieve new levels of efficiency.
This transformation would ultimately hinge on the investment of a new CNC machine – one which could both simplify and enhance production with cutting-edge capabilities. The machine in question is HOMAG’s CENTATEQ P-110 five-axis CNC Machining Center.
A setback
“This story begins dramatically, with the catastrophic failure of our existing CENTATEQ P-110 machine,” explains Julian McBride, Managing Director at Northern Fire Solutions. “It was our own fault; we were getting moisture into the machine via our compressed air system which caused the failure.” This left the company without a critical tool for an extended period.
“To bridge the gap,” continues Julian, “we decided to buy a budget machine imported to a UK retailer from China with four-axis technology. It served us for two and a half years but didn’t offer the flexibility we had with our existing CENTATEQ P-110 machine. We knew it was only a short-term solution, basically biding our time until we could get our hands on another HOMAG CNC.”
Why HOMAG?
Having previously experienced success with a HOMAG CNC machine, Northern Fire Solutions had no hesitation in turning to HOMAG for their next investment. Essentially they were buying the same machine as before – but with a few upgrades.
“We’d known for a while there were certain aspects of our old machine which needed either adding to or upgrading. So we went down to see HOMAG UK and discuss our needs. Their knowledge and expertise were critical; we gave them a brief and they were able to make their recommendations accordingly. We took their advice and, as you’d expect, it was spot on.”
Software integration was another key factor in their decision. As Julian explains, “We use an ERP software system CalWin, and they’ve collaborated with HOMAG to provide projectManager – a piece of software that sits very nicely between CalWin and the machine.”
Additionally, the company is implementing HOMAG’s productionManager, software that is not linked to CalWin but is designed to give detailed feedback from workstations on the factory floor. Julian adds, “productionManager will allow us to track which components and items have been processed at each workstation. This software provides feedback to our administration team offering us real-time insights into our production process.”
The company aims to have projectManager and productionManager, along with a new barcoding system, fully integrated by Q2 2025. “This will mean that utilising the projectManager software, we can convert manufacturing information from CalWin into precise programmes for the five-axis machines, which will be an incredible upgrade to our operation.”
Seamless installation and training
The CENTATEQ P-110 arrived as planned, and the installation process was smooth and efficient. “It was excellent,” reflects Julian. “HOMAG ensured every detail was accounted for, including access restrictions, to guarantee a hassle-free delivery. The machine was operational within days, just as planned.”
Brian from HOMAG stayed on site for an extra day to provide training. “As it was the same machine we didn’t require a full training programme, but there were a few different functions we needed to learn about. Brian went through everything and then stuck around to watch our guys operate the machine, to ensure they were comfortable with it. It was a seamless transition.”
Immediate benefits
Years after the failure of their old CNC machine, Northern Fire Solutions Ltd is now operating with unparalleled efficiency thanks to the additional CENTATEQ P-110. “During the period we were utilising the imported Chinese CNC, we were operating at full capacity, but not nearly as efficiently as we are now with our two near-identical machines.
“Previously, we had to pick and choose which machine handled certain tasks. Now, everything can be done on either of the CENTATEQ P-110’s. The software integration allows us to do that; with everything cross-pollinated, we can run all our programs at the push of a button, streamlining our workflow and making everything a lot easier.
“Moreover, thanks to the five-axis technology, our programmes don’t take as long to run. This newfound production speed has not only improved our service but has also significantly increased our capacity. We also expect to reduce machining times by approximately 30-40% by changing the machines.
“We’re delivering fire-rated doors with more efficiency – and precision – than ever before. We expect the machine to pay for itself in as little as one or two years.”
More than a machine
“The service is fantastic,” praises Simon Downing, Maintenance and Development Manager. “We’re on a first-name basis with a lot of the guys; we know that if we pick the phone up, there will be a friendly voice on the other end ready with a solution. And if we’re struggling to programme something, they’ll actually log in remotely and go through it with us. This level of care and attention makes such a difference.”
Team effort
With the HOMAG CENTATEQ P-110 fully operational, Northern Fire Solutions is well on the way to full digital transformation – and a new era of efficiency. The journey to this milestone, having begun with the misfortune of their old machine failing, was no small feat.
“Exceptional teamwork and planning were key,” says Julian. “I’d like to recognise the incredible efforts of our team: Simon Downing, our Maintenance and Development Manager, for expertly coordinating the installation project, and Liam Feetham, our Production Manager, for ensuring consistent production levels during the transition.”
The future looks even brighter as the company prepares to integrate HOMAG’s projectManager and productionManager software in Q2 2025. “We’re excited for what’s to come,” concludes Julian, “and as we continue to deliver exceptional quality while scaling capacity to meet growing demands, we’re very glad to have HOMAG by our side.”
For more information or a demonstration of any of the HOMAG machinery and software, contact Adele Hunt at HOMAG UK on 01332 856424.
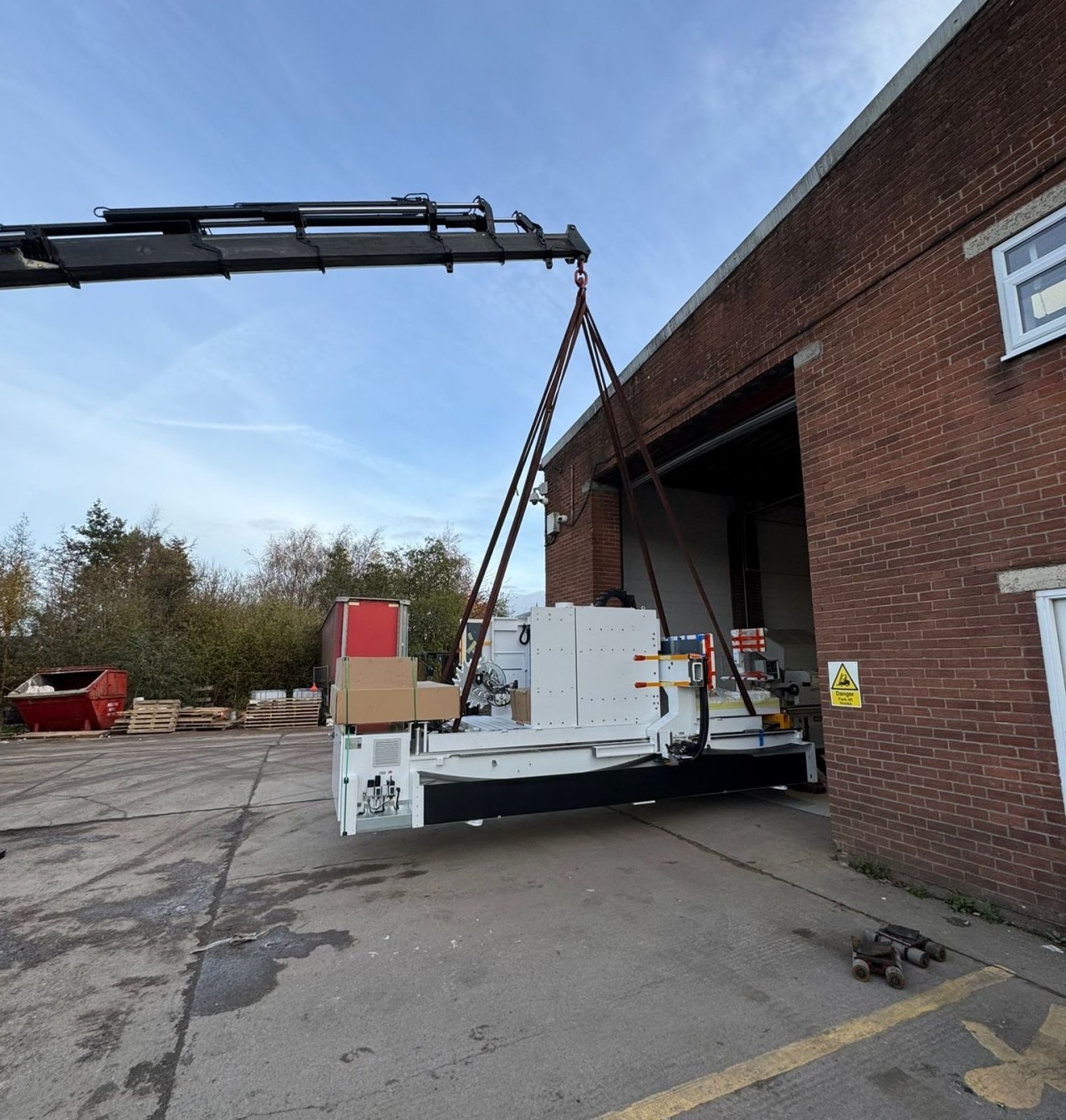