At Riverside Wood Products Ltd, in Darwen, Lancashire, Extractly Ltd has carried out a significant upgrade and reconfiguration of the company’s dust extraction system, including the installation of energy-saving ‘extraction on-demand’ technology.
Headed up by Paul Sullivan, RWP is a well-established, family-owned joinery shop offering a wide range of machining services. As well as processing high volumes of panels and ‘cut & edge’ boards, plus timber components in all shapes and sizes, the company also undertakes everything from carcassing and assembly work to individual bespoke furniture projects.
For over a decade, the company had enjoyed steady and continuous growth in the relative comfort of a 9,000 sq. ft. workshop. In more recent years, however, having invested in several new machines to keep pace with the demands of an ever-expanding order book, it’s fair to say the company’s workshop was bulging at the seams. So, in early 2024, when the adjacent warehouse space unexpectedly became vacant, Paul Sullivan took the decision to literally ‘knock through to next door’ and has more than doubled the available floor space.
The now vastly-improved production facility includes an impressive line-up of Homag machinery; including several CNC machining centres, plus a couple of edge banders, as well as a horizontal beam saw. “When all these high-speed machines are in operation, the need for an equally efficient dust extraction system is obviously essential”, says Paul Sullivan, “and this reorganisation of the factory presented us with the perfect opportunity to upgrade and reconfigure the system as we relocated the various machines.”
Extractly’s sales director, Jake Oldfield, had initially been invited to assess the company’s requirements for a completely new extraction system, including the supply and installation of a new filter unit. Subsequently, however, following the winding down of production at L&G Modular Homes’ factory in Yorkshire, and obviously with a keen eye for a good deal, Paul Sullivan had acquired a substantial pre-owned filter unit, complete with its 75kW main extraction fan. “Getting it transported across the Pennines and fixed securely in place here was the easy part,” Paul conceded, “but installing new ductwork throughout the factory, and getting the whole system to work safely and efficiently with a second-hand filter unit, was definitely a job best left to the professionals!”
“Although we’d had to forgo an order for a new filter unit,” says Jake Oldfield, “this was still a sizeable project for Extractly and, because the fan and filter Paul had installed was probably powerful enough to extract from a factory twice the size, our revised proposal also included for the supply and installation of Ecogate® energy-saving ‘On-Demand’ extraction control technology.”
Without Ecogate® installed, the main fan would be operating at full power, throughout the working day, with a total annual electricity consumption estimated at around 180,000kW.
However, with an Ecogate® greenBOX controller continuously monitoring individual machine usage and, via the Ecogate® PowerMASTER™, continually adjusting fan speed to exactly match extraction demand, huge reductions in electricity consumption are possible – resulting in correspondingly significant cost savings, as Paul confirmed: “Although the fan’s motor has the capacity to give us up to 75kW worth of extraction power, the Ecogate® system provides real-time data on power consumption and typically, with most machines running, we’re only using around 35kW … but that then reduces at break times, as machines are powered down, and once all machines are shut down the fan also shuts down automatically.” And, as Paul also points out: “The workshop is a much calmer, quieter place to work than it used to be!”
Although the Ecogate system is configured to control electricity usage at current production levels, it has more than enough capacity in reserve to continue providing efficient extraction if RWP invest in further new machinery. The Ecogate® greenBOX installed at Riverside is the highly intelligent ‘Nxt’ model, which has the capacity to control the operation of an extraction system with multiple main fans and up to 72 individual workstations, so the extraction system is now effectively ‘future-proofed’.
The Nxt controller has an industrial PC onboard, and a built-in web server provides remote access for fast, automated software updates. In addition, with systems controlled by a greenBOX Nxt, the processor integrated into each 24V DC motorised ‘Smart’ damper provides reports on pressure, air velocity, and air volume and, to ensure employees’ safety, minimal airflow is automatically managed across the entire ductwork system to reduce the risk of fire or explosion.
“I had a lot of confidence in the team from Extractly,” Paul explains: “In the past, we’ve probably been guilty of just going with the cheapest quote for extraction work, but once bitten, twice shy, and Extractly’s onsite installation engineers, led by experienced operations director, Graham Day, were a credit to the company.”
Extractly Limited
01924 520462
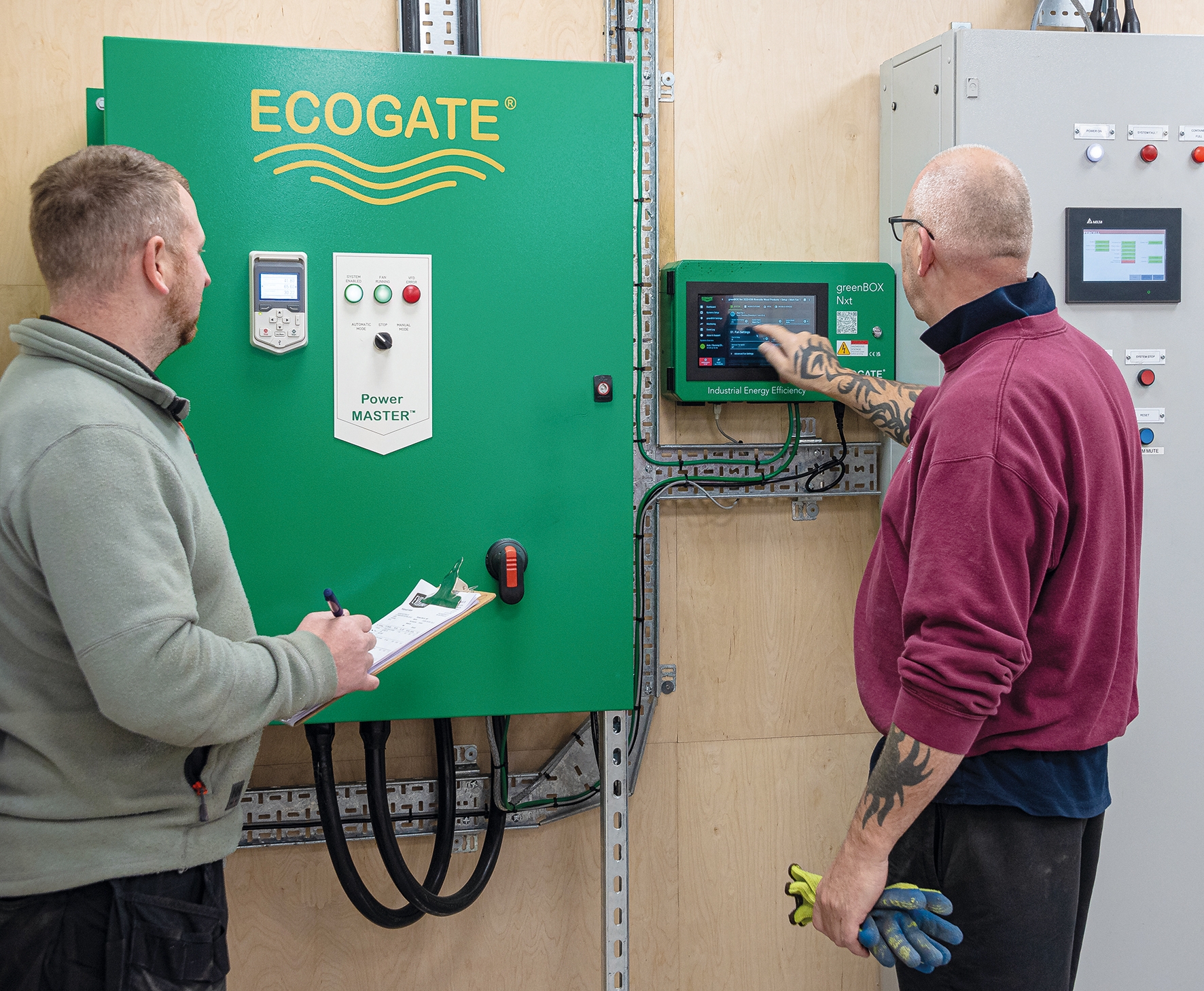
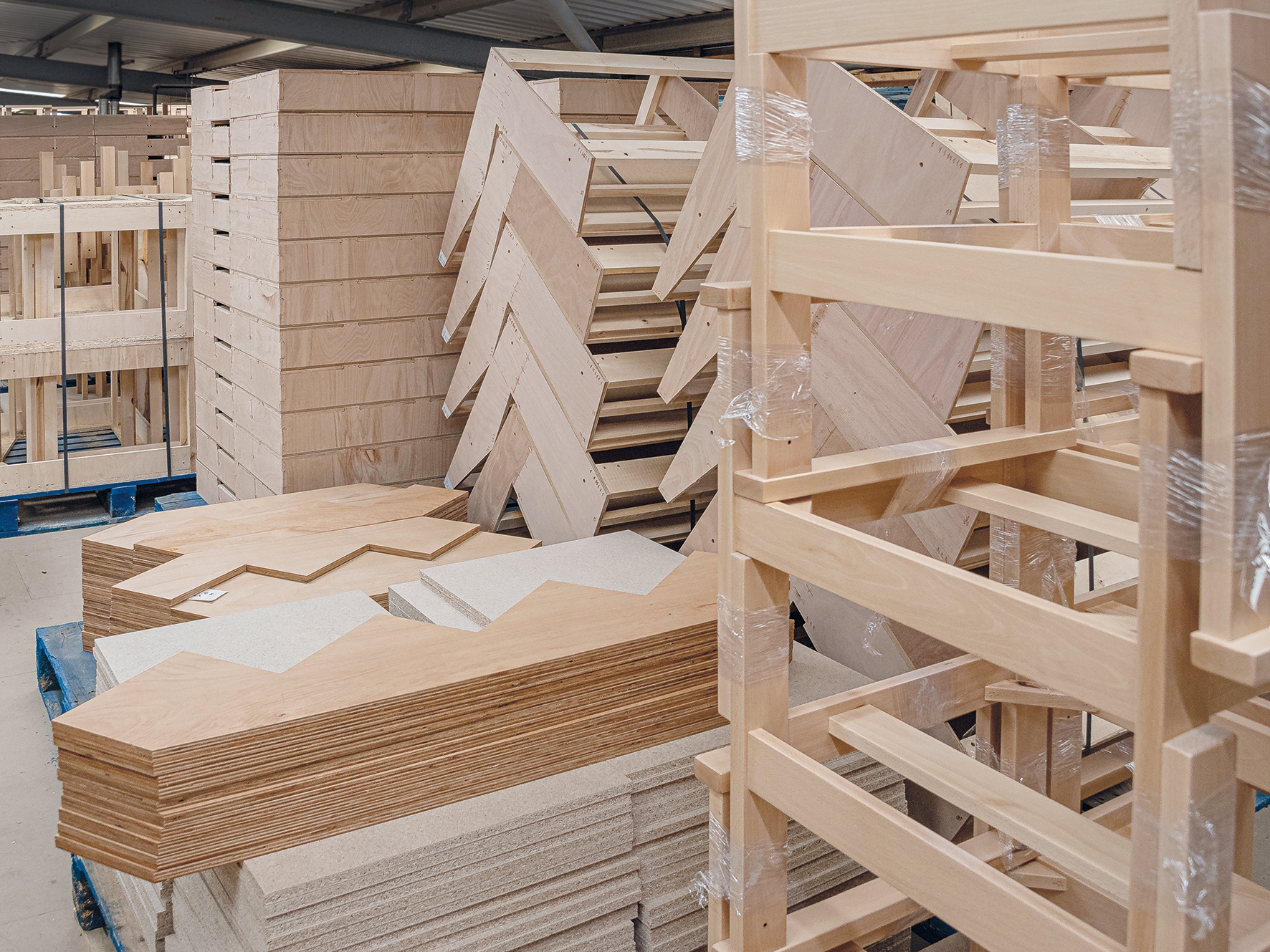