Founded in 2003, ar18 operates out of a 25,000 sq. ft. facility in Uxbridge, offering a comprehensive range of services – from retail furniture and display stands to bespoke, one-of-a-kind pieces. Their expertise spans CNC machining, joinery, paint spraying, metalwork, and printing, supporting clients from concept to final product.
As client expectations evolved and projects grew more complex, ar18 recognised the need to accelerate their design process and efficiently manage outputs across multiple CNC machines. Staying ahead in today’s competitive market required embracing cutting-edge technology and streamlining every aspect of their workflow.
Challenges that prompted a search for solutions
ar18 faced challenges common to many manufacturers: outdated tools and fragmented processes were slowing progress and creating unnecessary complexity. Routine tasks consumed significant time, delaying order processing and straining resources. Client demands for tailored product variations and repeat bespoke work further exposed the limitations of their existing systems, with design adjustments often leading to errors, increased material waste, and extended production timelines.
The need for a smarter, more connected solution – one that could streamline workflows, improve accuracy, and enable faster, more consistent results – became impossible to ignore.
Why Microvellum was the right fit
In 2023, ar18 implemented Microvellum Software, a decision that transformed their operations. “Microvellum has increased the speed and accuracy at which projects can be completed, and it’s hard to think of not having it,” shares Gurney Peterson, Design Manager at ar18.
One of the first advantages ar18 experienced was Microvellum’s seamless integration with AutoCAD. As an industry-leading CAD software used by millions of designers, drafters, and engineers worldwide, AutoCAD is a critical tool for creating precise 2D and 3D designs. With Microvellum, all the manufacturing data is embedded directly within the product drawings. Once their CAD designs are approved, projects can be sent straight to production without the need for additional steps, significantly saving time and minimising errors.
Microvellum’s open architecture brought unparalleled flexibility. “With Microvellum, we’re not limited by predefined products,” says Gurney. “No two joinery jobs are the same. With Microvellum, we bid on any project, engineer any design, and make almost anything. The flexibility means we’re never boxed in.” This adaptability has allowed ar18 to confidently take on diverse projects, from cabinetry and retail fit-outs to bespoke furniture for bars and restaurants. “The ability to access the backend of the products and work with the parametric logic provides much greater versatility compared to other software.”
A key to this success is Microvellum’s library data, which balances standardisation with customisation. It ensures consistent quality across projects while enabling tailored solutions for client-specific needs.
Transforming production and reporting
With three MultiCam 3000 CNC routers, two Weeke Vantage CNC machining centres, and a Homag STORETEQ, ar18 relies on precision machinery to maintain high-quality production. Microvellum’s direct integration with this equipment has streamlined processes, automating tasks from g-code generation to part optimisation and labelling. This seamless connection has maximised efficiency and precision while eliminating the need for additional third-party software.
Microvellum’s reporting tools have introduced a new level of efficiency and insight. With an integrated report designer and access to an open database, ar18 can generate detailed production reports for every project while also having the flexibility to create fully customised reports tailored to their specific needs. “The purchasing of materials, hardware, and our assembly and edge banding processes have improved with the various reports that can be produced,”
Additionally, Microvellum’s Solid Modelling Tools have expanded ar18’s capabilities. These tools allow users to analyse 3D models and assemblies to create CNC-ready products, ensuring precision and efficiency in production. By leveraging this functionality, ar18 has engineered and visualised highly customised products like display fixtures, bespoke bars, and restaurant seating. Whether working with AutoCAD models or importing designs from other software, ar18 ensures every part meets exact specifications, minimising errors and delays.
The ability to generate detailed reports and visualise complex designs has also enhanced communication with clients, fostering stronger relationships and greater transparency throughout the project lifecycle.
Growth and new opportunities
Microvellum has not only addressed ar18’s challenges but also set the stage for long-term growth. The software has empowered the team to confidently tackle complex and creative projects while providing a scalable solution to support their expansion into a state-of-the-art factory with cutting-edge machinery.
By embracing innovation and streamlining their processes, ar18 has improved efficiency and positioned itself to explore new markets and opportunities. Microvellum’s flexibility, precision, and robust tools have become integral to their ability to meet the demands of their diverse client base.
For ar18, Microvellum is more than just a software solution – it’s a trusted partner in their journey toward continued success. As they look to the future, the partnership is a cornerstone of their strategy for growth, enabling them to redefine what’s possible in modern manufacturing.
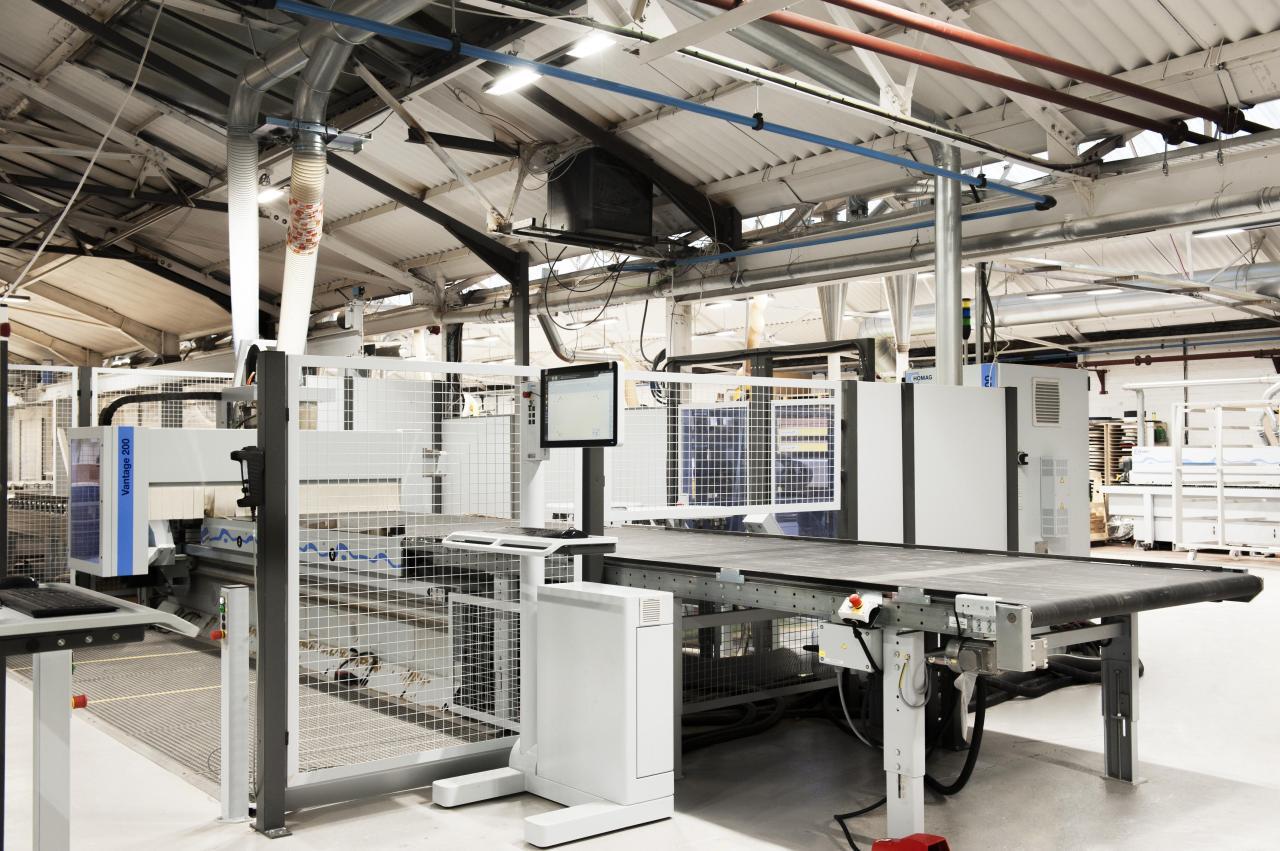
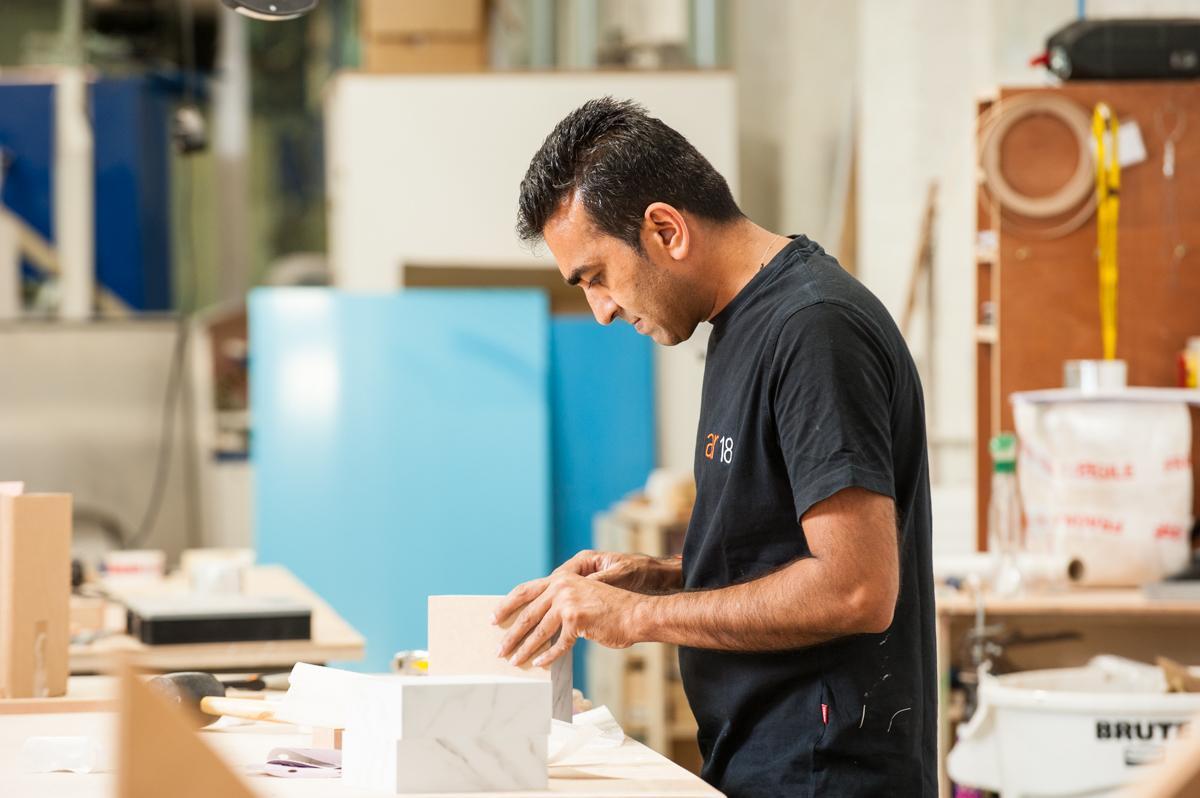
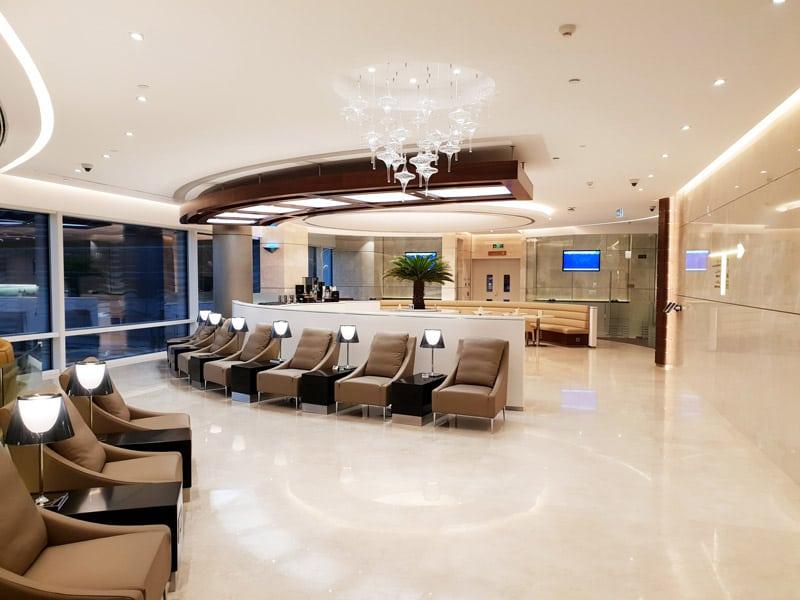