Specialist craftsmen and shopfitters have long understood the benefits of using Lamello fittings to join panels, especially when there’s been a need to assemble in the workshop, disassemble and fit on-site. However, according to Lamello, larger manufacturers haven’t caught on to the same extent. Most put the lower cost of glue and dowels forward as the reason – but at BeModern, they’ve worked out every aspect to the penny and their conclusions might come as something of a surprise ...
“Predominantly we make furniture for bathrooms,” BeModern Group’s design engineer, Gavin Potts, explains. “We have an entry level range, a mid-level range (which is our core business) and a couple of products that are in the high end of the market. The majority are sold through plumbers’ merchants and builders’ merchants, and most are made from MFC or MDF with a pressed PVC foil finish. Our furniture is designed to be fitter and installer-friendly. If you’re fitting or replacing furniture, installations should be possible within a day. We aim to make that possible more easily.
“I’ve worked at BeModern for almost 19 years and until recently we’ve always constructed with glue and dowels,” Gavin continues. “It worked for us at the time and it worked with the machinery we had, but machines have progressed. Three or four years ago, together with production director, Kevin Simpson, we started looking at ways of advancing our production and making it a lot more streamlined. We also wanted to make onsite work easier and faster for our fitters, so if any part of a product needed to be BeModern makes staggering time savings with Lamello fittings removed – for example, to make a cut-out in a back panel to accept plumbing or a basin without disassembling the rest of the cabinet – they could dismantle and reassemble a lot easier.
“We’d seen Lamello’s fixings at exhibitions and saw them as a way forward. When talking to machinery suppliers, the name that came up most often was Lamello, so, together with SCM and help from the Lamello representative, we decided to take the plunge and invest, starting when we launched our brand-new product line.
“The Lamello fitting we decided to use is the Cabineo. It is more expensive than the glue and dowels we were using, but when we did a cost exercise, we discovered the savings on labour and machining time more than balanced that out. Assembly takes half the time with Cabineo. Machining takes half the time. All machining can be done on one machine, so there was no transferring panels from one process to the next. Then there are time-savings and advantages for our fitters.
“Thinking ahead, if we were to offer flat pack alternatives at some point, construction would also be simpler for the end user because there would be fewer fittings and they are really easy to fix. We decided Cabineo would be a good option for both.
“With glue and dowel construction, we had to break everything out to 3mm, cut the long lengths, put them through the edgebander, then they’d go back through the saw. Then they would be cut into the shelf size – 400, 500, 600mm – before going back to the edgebander. Next came top drilling, and side drilling, and then the parts would go through to assembly. Using the Lamello fittings cuts all that out.
“We spoke to several machinery suppliers but the one that offered us the best solution was SCM, so we bought two Morbidelli X200s and a Stefani KD edgebander. Now, everything gets drilled on the Morbidelli before it’s edgebanded. Edgebanded components go straight through to the guys in assembly who knock the Lamello fittings in and assemble.
“Since we started using Lamello’s Cabineo, I don’t think we’ve had one complaint. At first, there was some hesitancy from the guys in assembly because it was something different and the Cabineo fixing needs an Allen key to tighten the bolt that fixes the panels, but the parts go together really easily and it’s quicker to assemble. Now all the guys love it.
“Our production times have really dropped because now with the Morbidelli X200s, we put a full pack of boards on, apply the nest, the machine feeds however many sheets we need through, cuts to the correct size, drills three holes to accept each Cabineo, labels and all the parts come off, ready for edgebanding and the insertion of fixings.”
SCM doesn’t supply a specific aggregate for the Cabineo, it’s a Cabineo macro embedded within the software. Every SCM machine equipped with Maestro software has the macro inside. The macro enables BeModern to apply the Cabineo fitting to their product with just the click of a button.
“We highlight the holes, click the depth we require, and it automatically puts three holes in to accept the fixing,” says Gavin. The macro for Cabineo has an option within it that allows the user to decide if they want to use a drill to machine the three 15mm diameter holes – BeModern’s preferred option – or use a 10mm diameter router tool to cut the pattern. Nothing specific beyond the preferred tool is required. Gavin admits that changing from glue and dowel, or cam and dowel to Lamello could have been difficult from a specification and stock control perspective because BeModern, like many large-scale producers, holds thousands of cabinets in stock in its warehouse.
“To have a mixture of stock within the warehouse would have been a headache,” he says, “But at the time we introduced Cabineo, we were on the point of launching a brand new range. We started the new range on the Lamello fixings and simultaneously discontinued the old product, phasing out the old fixings at the same time.”
Gavin has nothing but praise for the help BeModern has received from Lamello: “They gave us a lot of help with everything from choosing the right fitting to tooling for the machines. With the Cabineo fittings, there’s a special Allen key that comes with the fixing. Lamello provided them for us as a start-up cost-saving to get us up and running. They also gave us some fittings to see how we got on with them and that really helped when we were prototyping the new range. It’s much quicker to get prototypes through with the Lamello fixing.
“In terms of supply, we’ve had no issues with Lamello at all. Every time we order, they always have stock. We tend to try and keep two or three months-worth of stock on site in case there are any hiccups but we’ve never had any “Moving to Lamello has really streamlined our production,” concludes Kevin, production director. “The way we were set up before was for big batches – 200, 500 off. Nowadays, everyone wants small batches or one-offs and no one wants to hold stock. Using separate drilling machines, the cost in time alone for setting them up was enormous. If it was a manually-set machine, each drill could take 20 minutes to set up and we had horizontal and vertical drills. With some of the other machines, we were constantly putting jigs on and taking them off. If we made 10 batches a day, we were wasting hours in setting-up time alone.
“Just the time-saving from switching over from glue and dowels to Cabineo has given us a massive gain in production. That time-saving more than compensates for the extra cost of the fitting. It’s been a good move for us, really good.”
Contact Shaye Chatfield at Lamello to discover how, as a large furniture manufacturer, you can boost productivity and save time on production, assembly, and fitting by using the right fixings.
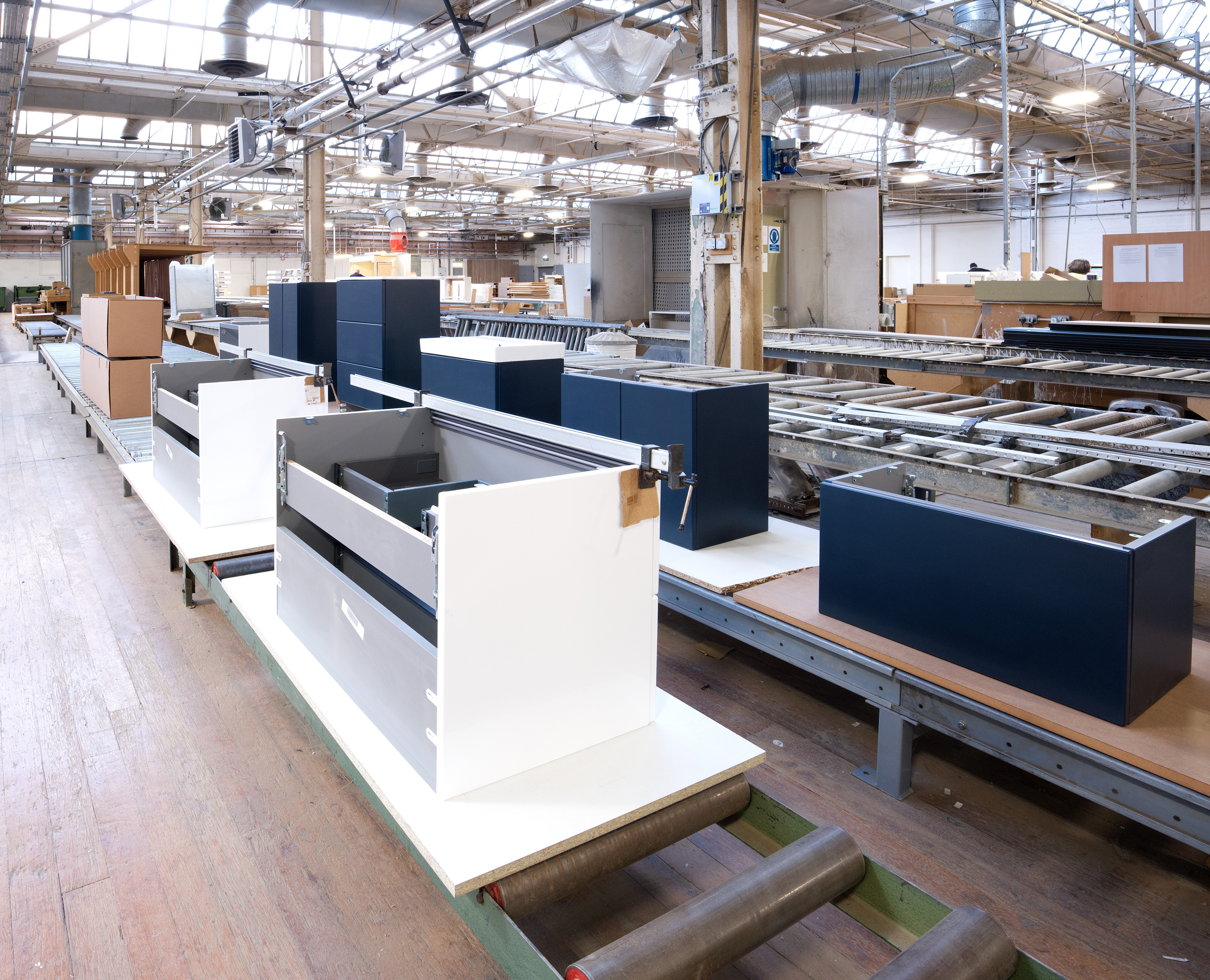
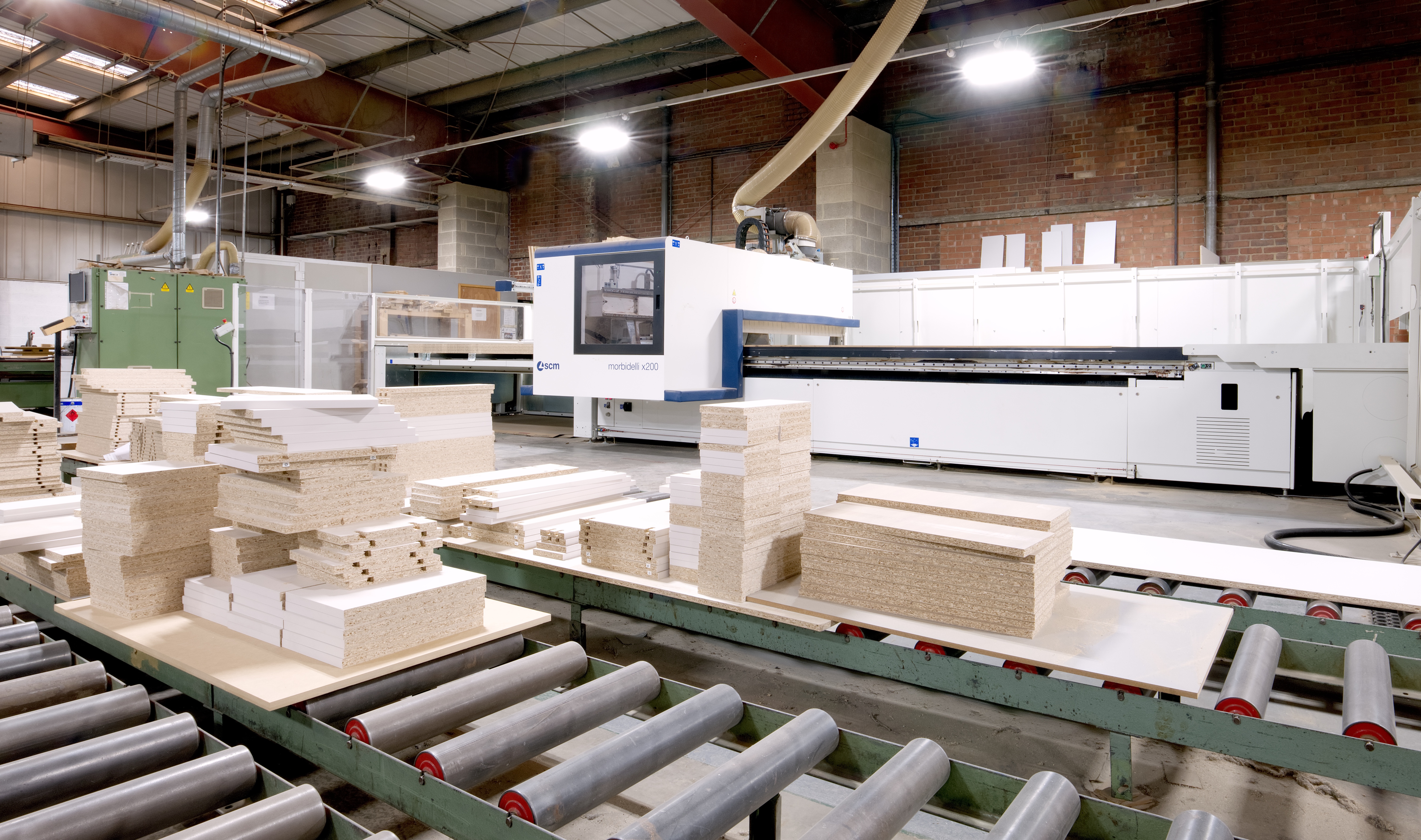
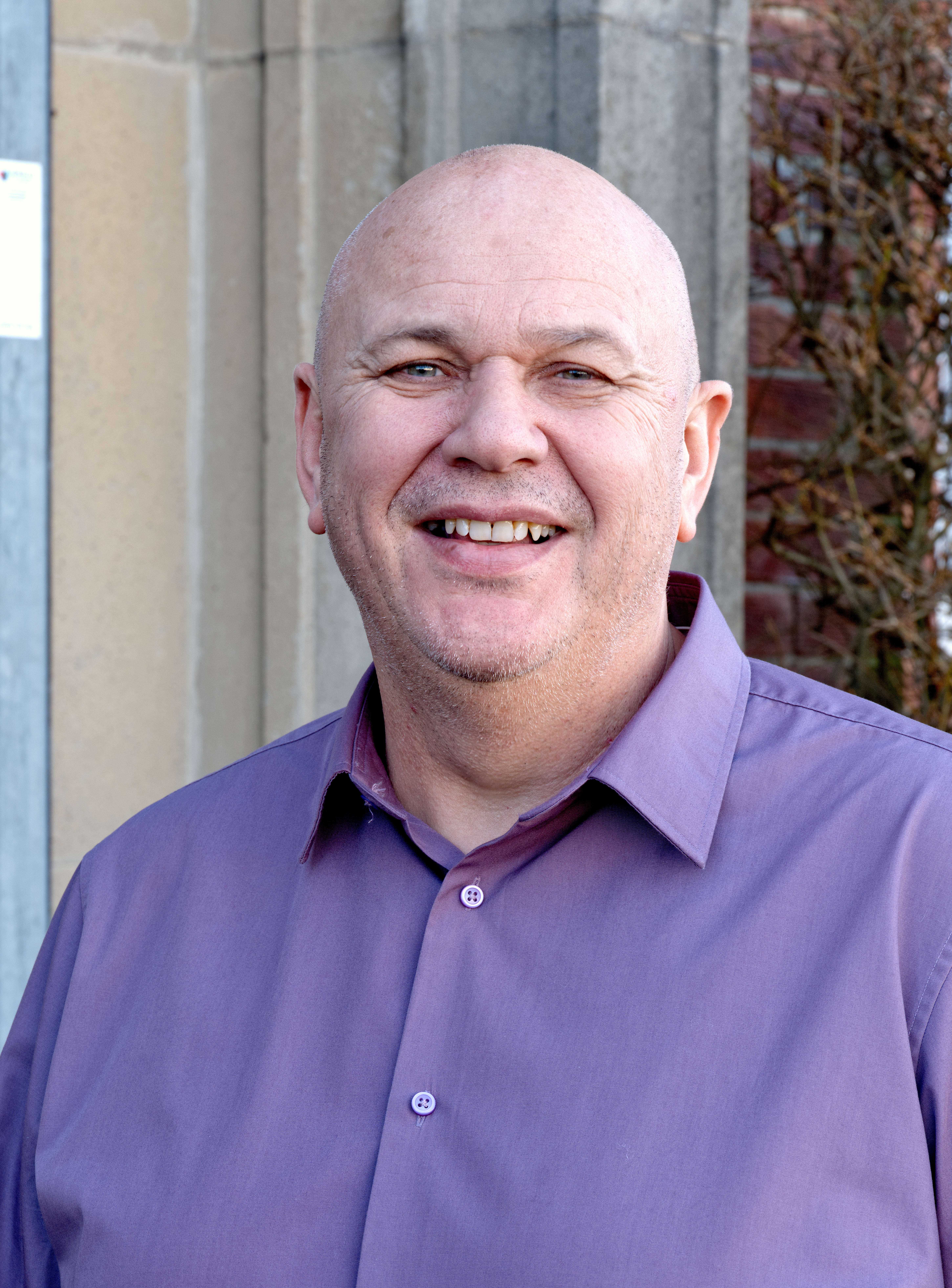
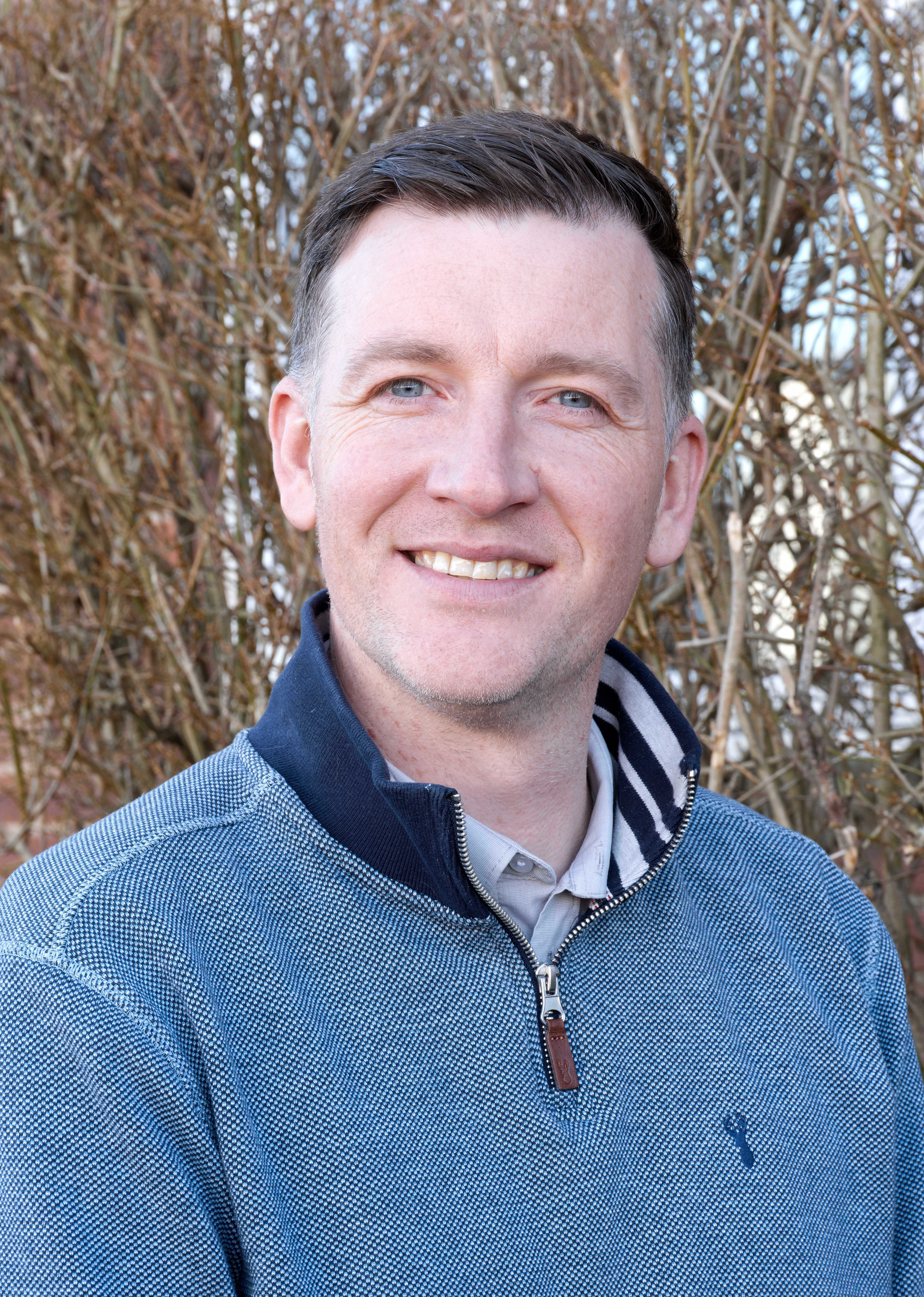