Based in Wrexham, CIBOR Woodworking Machinery Ltd. is a leading UK-wide supplier of high-quality woodworking and timber processing machinery. Here, we speak to Paulina Skrzypczak, Marketing and Business Development, about the company’s impressive portfolio of CNC automation and robotics solutions ...
Could you provide a brief overview of CIBOR Woodworking Machinery’s portfolio?
We offer a comprehensive range, including CNC machines, robots, SIP panels production lines, sawmills, finger jointing lines, door and window production lines, finishing machines, cross-cut saws, and beam saws. At CIBOR, we deliver solutions designed for precision, efficiency, and adaptability.
What would you say gives CIBOR Woodworking Machinery a unique edge in the market?
What sets CIBOR apart is our commitment to personalised, tailored solutions. We offer machinery that balances automation, flexibility, and cost-effectiveness, ensuring our customers achieve maximum efficiency while maintaining superior craftsmanship. Our strong partnerships with top-tier manufacturers allow us to provide robust, durable, and innovative equipment backed by expert support and a customer-first approach.
Could you discuss CIBOR’s current capabilities with regards to CNC automation and robotics?
At CIBOR, we see CNC automation and robotics as the future of woodworking, offering greater efficiency, precision, and flexibility. Our range includes not only multi-axis CNC machines, like CNC routers, milling machines, lathes, drilling and nesting machines, but in particular modern robotic stations tailored for furniture and pallet production and automating tasks such as material handling, sanding, finishing, and precision placement, increasing efficiency and consistency in production.
The robots we offer are versatile, easy to program, and ideal for both serial production and small batches. By embracing automation, we aim to provide our customers with smarter, faster, and more reliable woodworking technology.
What is CIBOR’s perspective on the merits of industrial robots as an alternative to traditional woodworking machine tools?
Integrating robots into the production process increases efficiency without needing to expand the workforce. Robots are particularly effective in automating repetitive, labour-intensive tasks, reducing errors, shortening production cycle times, and enhancing product consistency.
While traditional woodworking machines remain essential for certain applications, incorporating industrial robots offers greater flexibility, more optimised workflows, and significant productivity gains.
Could you speak more specifically on the robotic opportunities available in the furniture manufacturing & joinery fields?
Kitchen furniture: Robotic systems automate processes like loading/unloading CNC machines, and packaging.
Upholstered furniture: Robots are used for nailing frames, applying glue and upholstering.
Pallets and garden furniture: A robotic pallet production system offers speed, simplicity, and flexibility, eliminating the need for manual operation and preventing workplace injuries.
Bed production: Robots for nailing furniture frames provide speed and efficiency, reducing the hard work and time required for manual stapling.
Joinery & carpentry: Robotic assistance in drilling, sanding, and finishing ensures consistent quality across operations.
Are there any upcoming launches or developments that you’d like to discuss?
We are continuously working on expanding our product offerings and advancing our robotic and automation capabilities. Stay tuned for more updates as we continue to bring the latest technologies to the UK woodworking market. For more details, visit our website – www.cibor.co.uk
Robotics and automation are key to improving margins, optimising labour, and achieving a quick return on investment. Implementing this type of technology gives companies a competitive edge in the market. Contact us today to discover the best solution for your business.
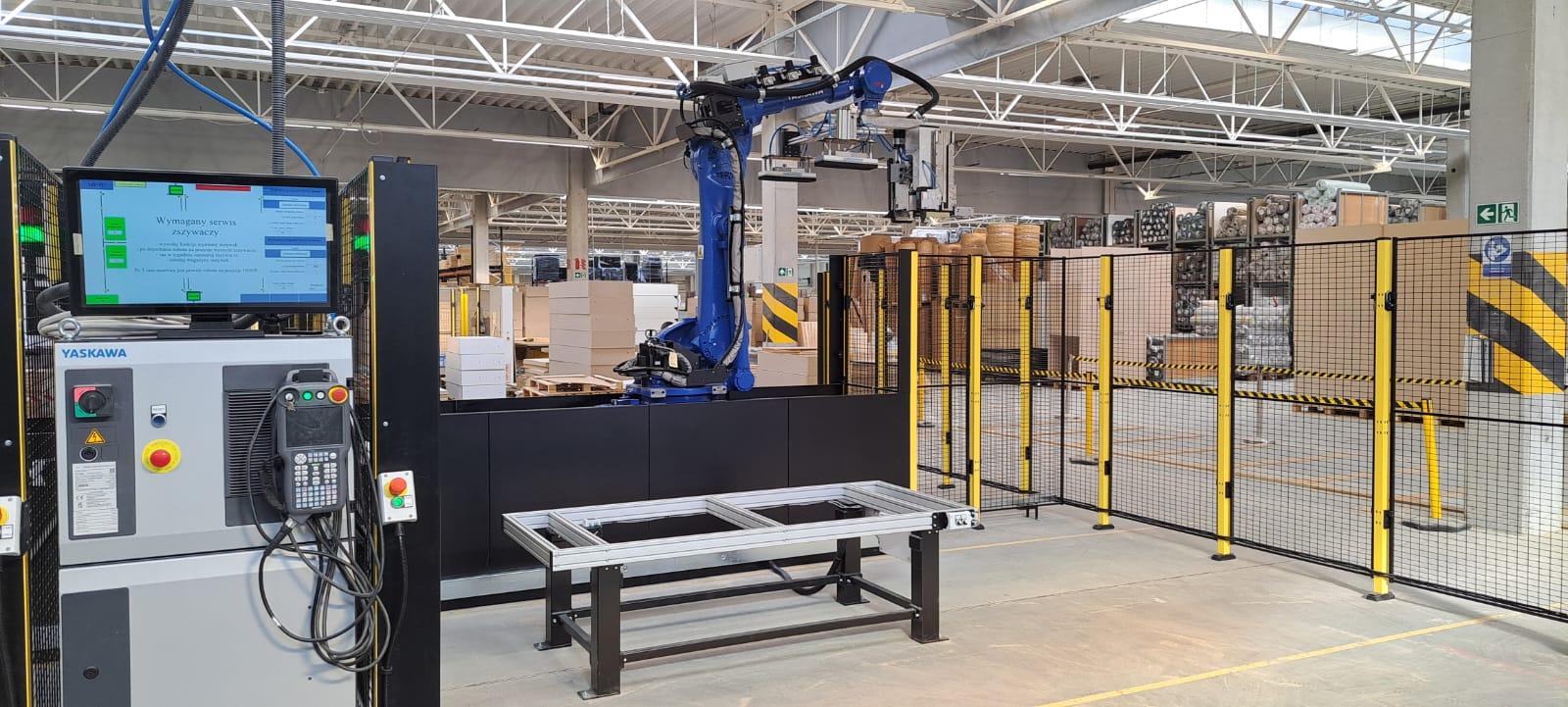
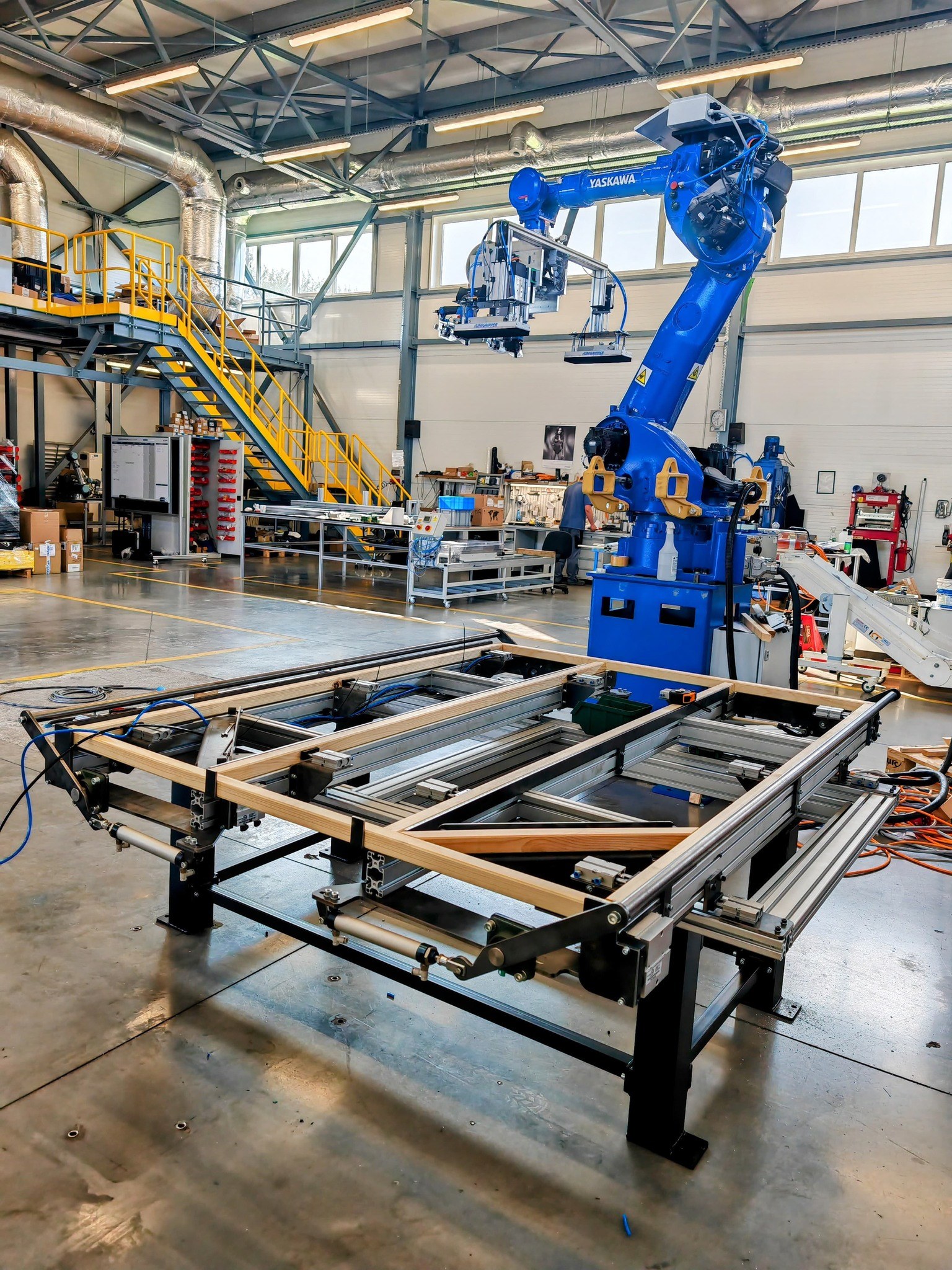